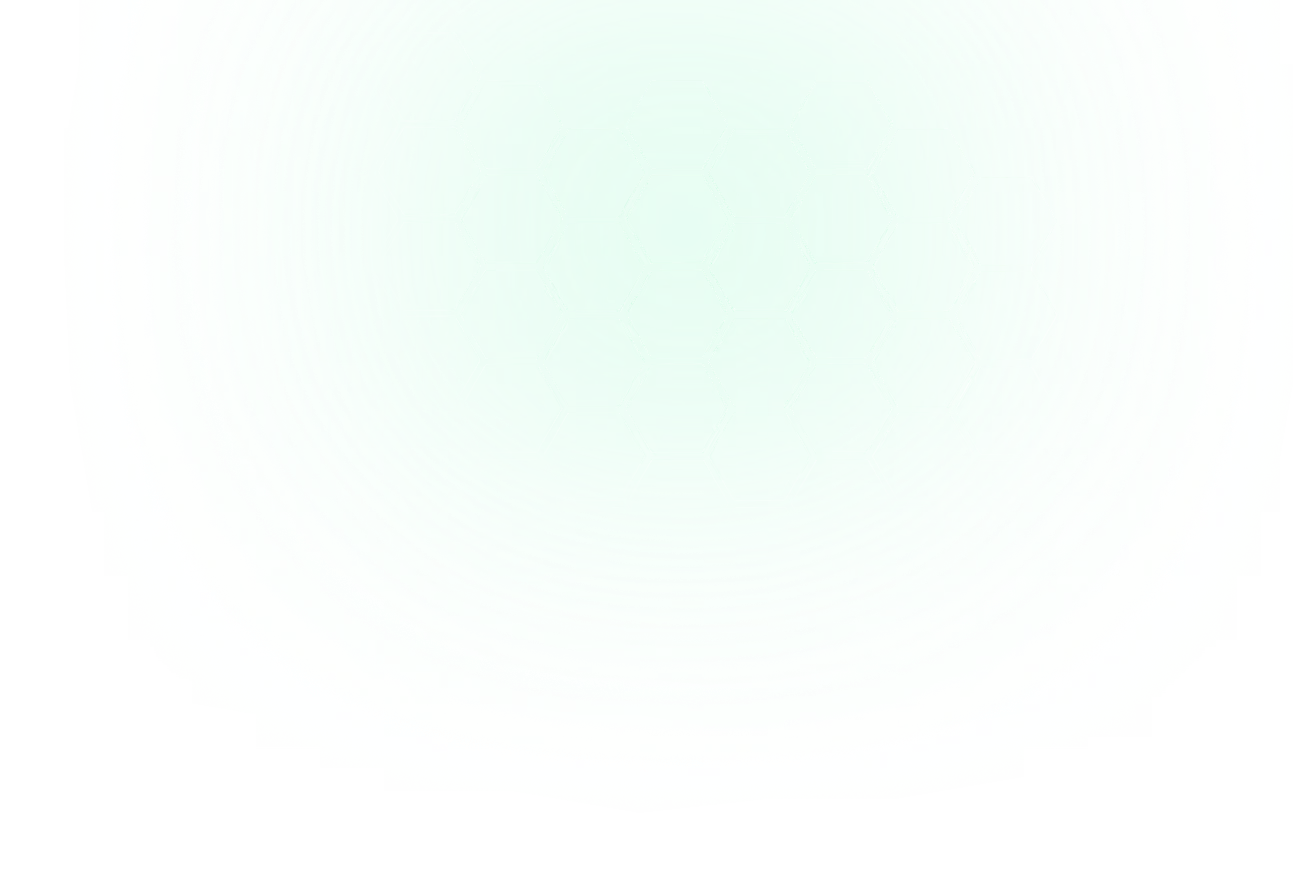
Hire Offshore Quality Engineers in the Philippines & Colombia
Manufacturing and engineering businesses face mounting pressure to maintain product quality while controlling costs and meeting tight deadlines. Quality control processes are often resource-intensive, requiring specialized expertise that can strain internal teams and delay production timelines.
At NeoWork, we provide dedicated quality engineers from the Philippines and Colombia who become integral members of your production team. Our offshore quality professionals bring rigorous testing methodologies, regulatory compliance expertise, and systematic quality control processes that protect your brand reputation while optimizing manufacturing efficiency.
When you partner with NeoWork to outsource quality engineering staff, you gain:
- Up to 70% cost savings compared to hiring local quality engineering personnel
- Certified professionals with extensive experience in manufacturing quality standards
- Comprehensive testing capabilities across multiple industries and product types
- Consistent quality oversight that scales with your production requirements
- Flexible scheduling to support global manufacturing operations
- Transparent pricing with straightforward monthly rates
Unlike temporary contractors or consultants working across multiple projects, our quality engineers work exclusively with your organization, developing deep familiarity with your products, processes, and quality standards.
Why Hire Quality Engineers with NeoWork?
1. Advanced Quality Control Expertise
Modern manufacturing quality control requires sophisticated technical knowledge and systematic approaches. When you outsource quality engineering through NeoWork, you gain access to professionals skilled in:
- Statistical process control (SPC) and Six Sigma methodologies
- ISO 9001, ISO 14001, and industry-specific quality standards
- Advanced testing equipment operation and calibration
- Root cause analysis using fishbone diagrams and 5-why techniques
- Quality management system documentation and maintenance
- Supplier quality auditing and vendor assessment protocols
These technical capabilities allow our quality engineers to identify potential issues before they impact production while maintaining the documentation standards required for regulatory compliance.
Our teams stay current with evolving quality standards through regular certification programs, keeping your quality control processes aligned with industry best practices.
2. Comprehensive Testing and Validation
Quality engineering extends beyond basic inspection to include systematic testing and validation processes. Our quality engineers handle:
- Incoming material inspection and supplier quality verification
- In-process quality monitoring and statistical sampling
- Final product testing and certification documentation
- Non-conformance reporting and corrective action planning
- Quality data analysis and trend identification
- Customer complaint investigation and resolution
This comprehensive approach protects your brand reputation while reducing the risk of costly recalls or compliance violations.
3. Regulatory Compliance and Documentation
Manufacturing businesses must navigate complex regulatory requirements that vary by industry and market. Our quality engineers maintain:
- Current knowledge of FDA, CE, and other regulatory standards
- Detailed quality documentation and traceability records
- Audit preparation and regulatory submission support
- Change control processes for product modifications
- Quality training documentation for manufacturing staff
- Continuous improvement tracking and reporting
This regulatory expertise reduces compliance risks while supporting your expansion into new markets or product categories.
4. Cost-Effective Quality Assurance
Quality engineering represents a significant operational expense that can impact manufacturing profitability. Our offshore quality engineers provide:
- Dedicated quality oversight without the overhead of full-time local hires
- Scalable quality support that adjusts to production volume changes
- Access to specialized testing equipment and software tools
- Reduced training costs through pre-qualified professionals
- Lower turnover rates compared to traditional quality staffing
This cost structure allows you to maintain rigorous quality standards while preserving manufacturing margins.
Our Quality Engineers Services
Quality Control and Inspection
Systematic product testing, material verification, and process monitoring to maintain consistent quality standards across all production activities.
Regulatory Compliance Management
Documentation, audit preparation, and regulatory submission support to meet industry standards and government requirements.
Supplier Quality Assurance
Vendor assessment, incoming material inspection, and supplier performance monitoring to maintain quality throughout your supply chain.
Quality System Development
Quality management system design, documentation, and maintenance to support continuous improvement and operational efficiency.
Statistical Process Control
Data analysis, trend identification, and process optimization using statistical methods to predict and prevent quality issues.
Why Staff Quality Engineers from the Philippines and Colombia?
Both the Philippines and Colombia offer exceptional talent pools for quality engineering roles, with strong educational systems producing skilled professionals who understand international quality standards and manufacturing processes.
Quality Engineers from the Philippines
The Philippines has developed a robust manufacturing sector with particular strength in electronics, automotive, and medical device production. Filipino quality engineers bring:
- Strong English communication skills for international manufacturing operations
- Extensive experience with ISO standards and regulatory compliance
- Technical education backgrounds in engineering and quality management
- Cultural familiarity with Western business practices and quality expectations
- Proven track record in high-precision manufacturing industries
The Philippine manufacturing sector's focus on export markets has created a workforce skilled in meeting international quality standards and regulatory requirements.
Quality Engineers from Colombia
Colombia's growing manufacturing sector and proximity to North American markets have produced quality engineers with specialized expertise in:
- Bilingual communication capabilities for diverse manufacturing teams
- Experience with both US and international quality standards
- Strong analytical and problem-solving skills
- Understanding of lean manufacturing and continuous improvement methodologies
- Flexibility to work across multiple time zones for global operations
Colombian quality engineers bring particular value to companies serving both domestic and international markets.
Get Professional Quality Engineering Support from NeoWork
Protect your brand reputation with NeoWork's specialized quality engineers from the Philippines and Colombia. Our quality professionals implement systematic testing and compliance processes that reduce manufacturing risks while supporting operational efficiency.
Based on our experience providing customer experience and virtual assistant services to manufacturing businesses, we've developed a quality engineering approach that delivers measurable value:
- Careful selection of quality engineers with relevant industry and regulatory experience
- Thorough onboarding to your products, processes, and quality standards
- Regular quality reviews of testing methods and compliance documentation
- Ongoing professional development in emerging quality management techniques
- Responsive project management that adapts to changing production requirements
Our onboarding process typically requires 2-3 weeks, during which your quality engineers learn your manufacturing processes, quality standards, and regulatory requirements. This preparation period allows them to provide effective quality oversight from their first active week of work.
Stop risking product quality while your internal team handles routine operational tasks. With NeoWork's quality engineers, you can maintain rigorous quality standards while focusing on strategic manufacturing initiatives.
Contact us today to discuss your specific quality engineering needs and learn how our expertise can support your manufacturing objectives.
Frequently Asked Questions About Quality Engineers
What industries do your quality engineers have experience with?
Our quality engineers have worked across diverse manufacturing sectors including electronics, automotive, medical devices, consumer goods, and industrial equipment. We carefully match engineers based on your specific industry requirements and regulatory standards. Many of our professionals hold certifications in ISO 9001, Six Sigma, and industry-specific quality standards. During the selection process, we prioritize candidates with direct experience in your product category and familiarity with relevant testing procedures and compliance requirements.
How do you ensure quality engineers understand our specific standards and processes?
We implement a comprehensive onboarding program that typically spans 2-3 weeks, during which your quality engineers learn your manufacturing processes, quality standards, and regulatory requirements. This includes detailed training on your quality management system, testing procedures, and documentation requirements. Our quality engineers also participate in regular training sessions to stay current with evolving industry standards and best practices. For more details on our onboarding approach, visit our How We Work page.
Can your quality engineers handle regulatory compliance and audit preparation?
Yes, our quality engineers are experienced in regulatory compliance across multiple industries and markets. They maintain current knowledge of FDA, CE, ISO, and other regulatory standards relevant to your business. Our professionals can prepare audit documentation, support regulatory submissions, and maintain the detailed records required for compliance. They also assist with internal audits and continuous improvement initiatives to maintain certification status.
What happens if our production volume changes significantly?
Our flexible staffing model allows you to scale quality engineering support based on your production requirements. Whether you need additional quality engineers during peak production periods or want to adjust coverage during slower periods, we can accommodate these changes quickly. This scalability is particularly valuable for businesses with seasonal production cycles or those experiencing rapid growth. Our transparent monthly pricing structure makes it easy to budget for varying quality engineering needs.
How do your quality engineers integrate with our existing manufacturing team?
Our quality engineers work exclusively with your organization and become true extensions of your manufacturing team. They participate in production meetings, collaborate with manufacturing staff on quality issues, and report directly to your quality management leadership. We provide dedicated communication channels and project management support to ensure seamless integration with your existing processes. Unlike consultants working across multiple clients, our quality engineers develop deep familiarity with your products, processes, and quality culture.
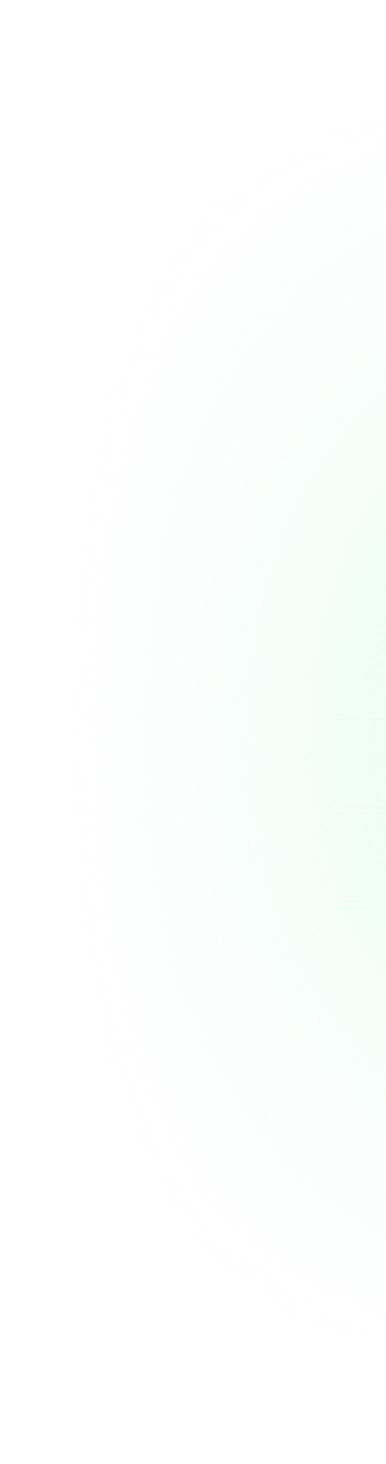
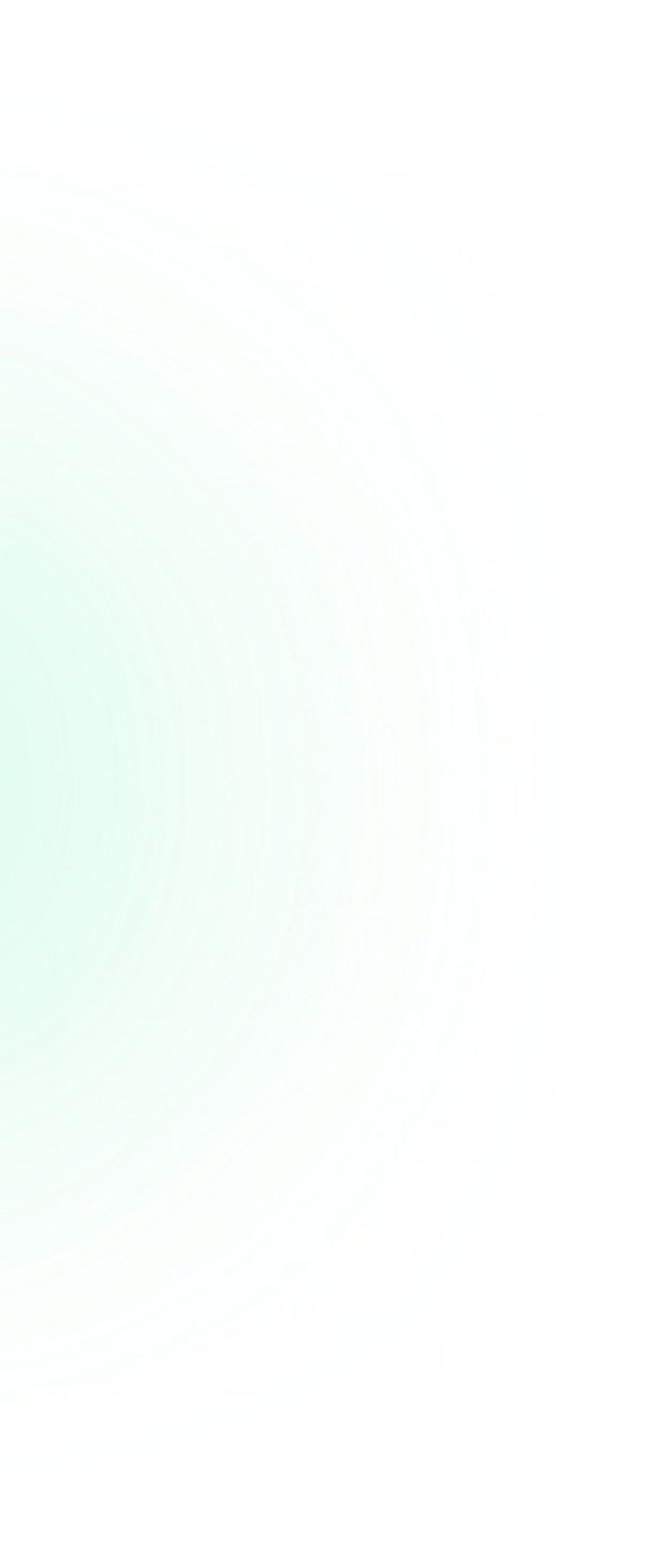